The texture of Chinese garden rockery stones: based on 3D point cloud and 3D printing technology

Introduction and previous research on texture recording and analysis
Studying the surface texture and morphology of cultural heritage sites is an important aspect of archeological research as it provides insights into the artistic, cultural, and historical significance of these sites. Surface textures can be particularly informative in helping archeologists uncover the esthetic and symbolic meanings embedded within cultural heritage, especially for those sites renowned for their distinctive surface textures1,2. In recent years, archeological methodologies have allowed for the development of various techniques for identifying and recording the textures of heritage surfaces3. These methods have proven invaluable not only for revealing deeper insights into heritage itself4,5 but also for facilitating accurate documentation6 and aiding in the preservation of cultural assets7,8. This research has opened new directions and possibilities for the broader field of archeology.
In China, the appreciation of rock textures holds a distinctive cultural significance that is deeply rooted in historical and philosophical traditions. The mainstream ideologies of Confucianism, Taoism, and Buddhism, which emphasize the important element of “the unity of heaven and humanity,” influenced Chinese classical garden designs. This cultural framework shaped the scholar-official class (literati) and cultivated a deep love for natural landscapes, which gradually spread, becoming a trend within the class. This esthetic appreciation transcended the personal realm, reflecting their political aspirations and serving as a source of solace when faced with career challenges. Consequently, both in their public roles and personal lives, the scholar-officials would turn to nature, giving rise to a cultural phenomenon known as “finding solace in nature,” which deeply influenced literature and art, fostering the development of landscape literature and landscape painting. The image of “mountains” became an enduring symbol in the minds of Chinese literati. As a result, landscape culture has become a cultural symbol of China. It was this admiration and reverence for mountains that inspired the scholar-official class to replicate natural mountains in gardens by stacking rockeries. As a result, rockeries also became a symbol of this culture. China’s tradition of stone appreciation dates back to ancient times. As early as the pre-Qin period (about 2200 years ago), stones were classified in the Classic of Mountains and Rivers9, identifying up to 42 different types. During the Tang Dynasty (about 1300 years ago), Chinese garden designs peaked, and the infiltration of poetry and painting began to directly affect the design of gardens. The technique of using stones to create rockeries has become more refined, with an increasing focus not only on the esthetic qualities of the stones themselves but also on their relationship with surrounding structures and the natural environment10. The tribute depicted in Yan Liben’s “Portraits of Periodical Offering” (Fig. 1) also includes mountain and stone bonsai. Stone culture peaked during the Song Dynasty (about 1000 years ago). During the Song Dynasty, the manufacturing industry in the Jiangnan region of China developed, and the Suzhou region was rich in supply of lake stones. These two conditions laid the foundation for the development of gardens and large-scale stacking of stones in the Jiangnan region. In the culture of appreciating stones, in addition to their shape, there is also an appreciation of stone patterns. The famous Chinese philosopher Su Shi of the Song Dynasty emphasized that the texture and irregular elements of stones together constitute their beauty. The texture of stones, particularly the surface textures of mountains, inspired the texturing method in Chinese landscape painting, where the physical forms were translated into artistic techniques11. This method, rooted in the painter’s observation of nature and self-reflection, has evolved into a unique symbol practiced by Chinese literati painters throughout history, ultimately forming a unique symbol of Chinese landscape painting. As a painting technique, the “texturing method” officially matured and developed from “texturing” to “texturing method” in the Ming Dynasty (about 600 years ago). In the Ming Dynasty, garden craftsmen began to follow the texturing method of garden designs, with rockeries built to reflect natural mountains’ physical and spiritual essence12. According to the numerous records of stacking rockeries using the texturing method, the significance of texturing for rockeries is significant. However, owing to a lack of geological knowledge, no scientific language for describing mountains exists, and only painting, as a language, can be used to explain them. Therefore, during this period, private gardens in Jiangnan relied on texturing to explore the style of stacking rockeries in gardens12. The “texture” represents nature derived from the love of Chinese people for mountains and rocks, which is the highly condensed and reproduced texture of mountains and stones and is reflected using the extremely fine surface texture of stones on the one hand. On the other hand, it reflects the overall shape and momentum of the mountains outlined by the lines in the stones. Since the Ming and Qing dynasties, concerning the stacking of rockeries, reference has been made to the “texturing method” in landscape paintings to stack rockeries. By coordinating stones and buildings in a limited space, it is hoped that the form and spirit of real mountains in nature can be expressed in garden spaces, thus realizing the cultural symbol of “the unity of heaven and humanity.” Therefore, studying surface texture and morphology in archeological research on garden heritage sites can help archeologists understand Chinese art and philosophy throughout history, which is an important part of archeology.
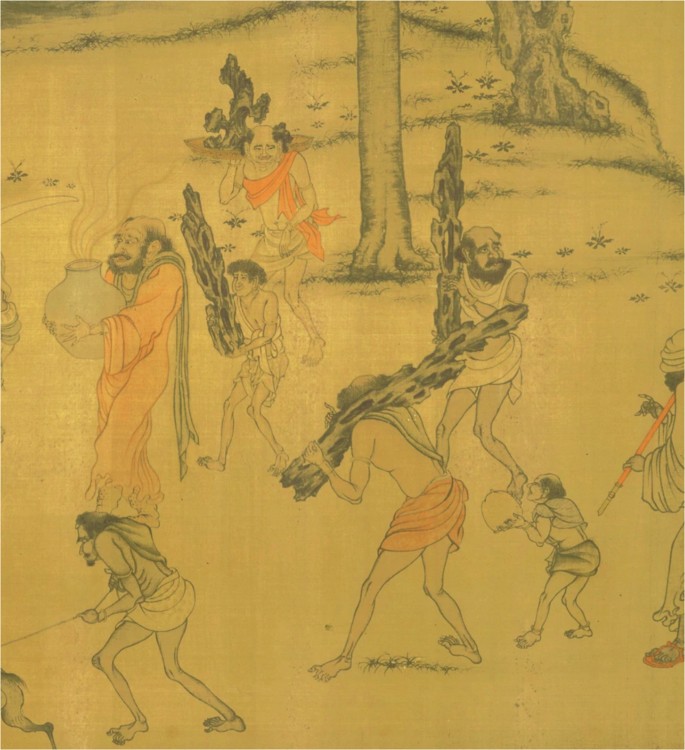
Part of Portraits of Periodical Offering.
From the above development process, we can see that “texture” is a way to reproduce nature derived from the Chinese love of mountains and rocks, reflected in their rockery and painting. Currently, most research on the special texture of rockeries is based on the study of the painting itself, thus comparing it with the surface texture of rockeries through a subjective judgment of painting and photos and recording of painting principles11,13. This research method cannot accurately identify the special textures of the rockeries themselves, resulting in slow progress in research on rock surface texture and morphology. The large size, immobility, and complex environment of this type of cultural heritage hinders the public’s understanding of it and its external dissemination. This poses a significant obstacle to the dissemination and research of the value of the heritage site itself, limiting the progress of archeological research on garden rock cultural heritage.
With the emergence of more interdisciplinary research methods targeting archeology and cultural heritage14, attempts have been made to use digital technologies and means to study the archeological records of rock cultural heritage. A large amount of research has proven that digital preservation technology is superior. Remondino et al.15 discussed the significant contribution of digital technology to the preservation of cultural heritage data; Hu et al.16 used stone cultural heritage as an example to illustrate that digital preservation technology can save cultural heritage that is being destroyed; and Li et al.17 emphasized that digital records can preserve the authenticity of cultural heritage and minimize intervention in cultural heritage.
There have also been numerous applications of digital technology in the field of heritage information analysis. Horn et al.18 attempted to use artificial intelligence methods to identify and analyze rock engravings. In contrast, Majid et al.19 reconstructed a realistic 3D model based on color information obtained through close-range photogrammetry, demonstrating the potential for recording and identifying rock surface textures in the context of cultural heritage and archeological research. Additionally, Kaya et al.20 contributed to different disciplines, such as archeology, by modeling and drawing cylindrical patterns at the Haran site in 3D, demonstrating the application of point-cloud technology in cultural heritage protection. Arnold et al.21 identified a heritage ontology from 3D point clouds using machine learning, demonstrating the feasibility of point-cloud technology in the digital research of rock cultural heritage. In addition, Yang22 introduced a cultural relic reconstruction device based on ORB-SLAM, which achieved multi-angle point cloud mapping of cultural relic scenes and could be extended to record and recognize the surface texture of large immovable cultural relics. Khorloo et al.23 focused on the virtual reconstruction of Karakoram ancient city, emphasizing the application of point-cloud technology in reconstructing ancient city ruins.
In recent years, there have been numerous cases of using immersive 3D digital technology to study heritage sites, such as Jo et al.24 attempting to use 3D technology for the reconstruction and restoration of heritage sites, Liu et al.25 discussing the feasibility of 3D technology in heritage site restoration, Zou et al.26 discussing the feasibility of immersive technology in enhancing public participation in heritage sites, and Niccolucci et al.27 systematically discussing the importance of digital twin technology in heritage management. Therefore, it can be seen that digital technology has extended from the initial data preservation of heritage sites to the management of and public participation in them. Digital technology has involved various aspects of heritage site protection and has become the main method and technological approach for its preservation.
Among numerous digital technologies, point cloud digitization technology has been applied to record and recognize the surface textures of rocks in various cultural relics, including cylindrical patterns, ancient cities, and large, immovable cultural relics. This study covers various fields, such as archeological sites, historical buildings, and cultural relics. However, in China, the current research in this field has mostly focused on applying 3D point-cloud technology to record and protect architectural heritage28. In recent years, photogrammetry and 3D point cloud recording methods have also emerged for the digital recording of garden rockeries, which mainly focuses on surface texture as a cultural value category29,30. However, no systematic or targeted research methods are currently available. Currently, most research focuses on digital recordings, and there is no specialized surface texture recording method for different rock types.
Consequently, for rock heritage sites with considerably high historical and cultural value, research on their surface texture is still primarily based on photos and paintings, which significantly limits the research process. 3D cloud technology can significantly outperform photography and painting in capturing the intricate details of rockery surfaces due to its ability to reproduce fine textures, maintain accuracy in measurements, and provide spatial analyses that provide a comprehensive understanding of rock morphology and its esthetic applications in landscape architecture. The texture on the surface of rocks is a type of information with three-dimensional spatial positional relationships. This three-dimensional spatial positional relationship is difficult to fully and meticulously display in painting. However, photos are constrained by shadow perspective relationships, making it difficult to fully record the texture content and conduct multidimensional analysis from different scales and angles. Our team has attempted to restore textures of Zhanyuan’s rockeries through 3D modeling using photos, but there is still a certain degree of deformation and scale difference31. Compared with recording methods such as photos and paintings, point-cloud data can indiscriminately recognize objects’ surface roughness and texture changes and are not affected by light and shadow interference. Based on this characteristic, it is possible to rapidly identify the overall shape and terrain of the rockery and perform a corresponding analysis. Therefore, this study begins with the perspective of digital recording methods. Digitizing different types of garden rocks and identifying their surface textures using stationary and handheld 3D laser scanners, respectively, and using 3D printing to replicate fake mountain stones with different materials. It selects three rockeries of different sizes—individual, integrated, and integrated garden rockeries—to ensure the recognition of various types of rock textures.
Materials and methods
Surface texture acquisition
The rockery stones in traditional Chinese gardens can generally be divided into two categories: integrated rockeries and individual rocks. Integrated rockeries are formed by stacking multiple stones to form a mountain with a certain volume, while individual rocks are usually single stones with extremely high ornamental value. To analyze rockery stones more clearly and comprehensively, this study focuses on studying these two types of rockery stones separately. At the same time, in studying rockeries with multiple stacked stones, local textures, and overall textures are studied separately, which can more comprehensively analyze texture types of different shapes and scales. Therefore, this study selected three fake mountain stones for research (Fig. 2).
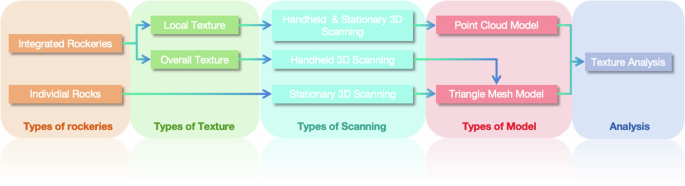
Flowchart for recording and analyzing surface texture of rockery stones.
Individual rocks: surface texture acquisition of Suzhou Ruiyun Peak
Ruiyun Peak (Fig. 3) has been known as one of the “Four Famous Stones of Jiangnan” since ancient times and represents the highest level of Chinese stone appreciation. Ruiyun Peak is 5.12 meters high, 3.25 meters wide, and 1.30 meters thick, with a base height of 1.13 meters and a total height of 6.25 meters. It is a huge artificial mountain rock. Owing to its location at Suzhou No.10 High School, it is not open to the public for most of the year and is located in the center of the pond, making it difficult to observe nearby. Therefore, although it is an important historical relic, there is little archeological research on this topic. Our team conducted much scanning and surveying work in the early research stage on traditional Chinese garden rockeries. Therefore, this study conducted surveying and scanning work based on the previous scanning process29.
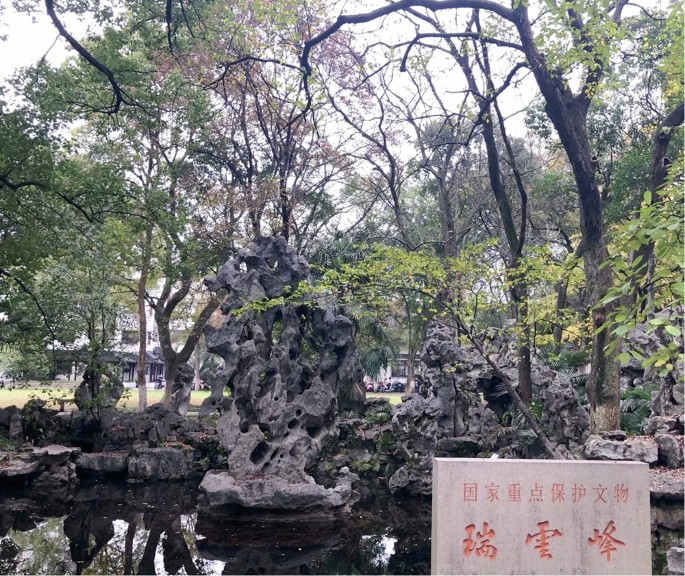
Ruiyun Peak.
Trimble TX8 (stationary) was used in this study with a collection accuracy of 1 mm and a scanning distance of over 335 m at a target reflectivity of 18%. The measurement speed was 1,000,000 points per second. Owing to the intersection and occlusion of various landscape elements and components in the rock, as well as the irregularity of the rock in the process of station construction, the number of measurement stations was increased during the scanning operation to comprehensively obtain the various faces of the rockery. Fourteen stations were built, and 105 million point clouds were collected (Fig. 4). Point-cloud data preprocessing was performed After the field data collection was completed. The Trimble Realworks (TRW) system software, which can process and concatenate point cloud data, was used for processing. During processing, after double calibration by manual splicing and automatic software splicing, excess and messy points, such as vegetation and buildings covering the surrounding areas, were removed, resulting in an actual processed point cloud quantity of 15 million. At the same time, we compared the accuracy level of the model under different point cloud densities. We found that the model with a quantity of 15 million was smoother than the model with a quantity of 6 million, which is more helpful in restoring the texture of the details of the rockery (Fig. 5).
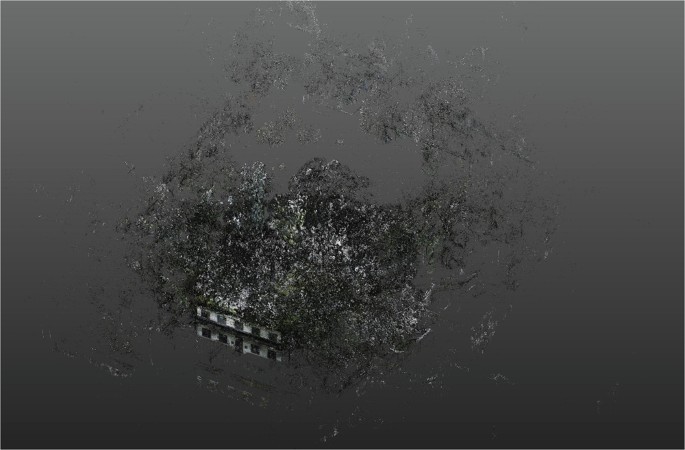
Point cloud of Ruiyun Peak.

Models with different quantity of points.
Triangulation modeling was performed based on the deleted point cloud, and local hole filling and trimming were performed according to the generated model, ultimately forming a complete Rayleigh Cloud Peak model. In this process, due to the presence of many plants in the surrounding environment of Ruiyun Peak, the software could not automatically recognize all plant point clouds. Therefore, it was necessary to combine computer automatic processing and manual screening for model processing in the modeling process. The final generated model maximized the texture restoration on the surface of the Ruiyun Peak with a processing accuracy of 1 mm (distance between points in spatial sampling). The texture and structural features of the rock surface were observed (Fig. 6).
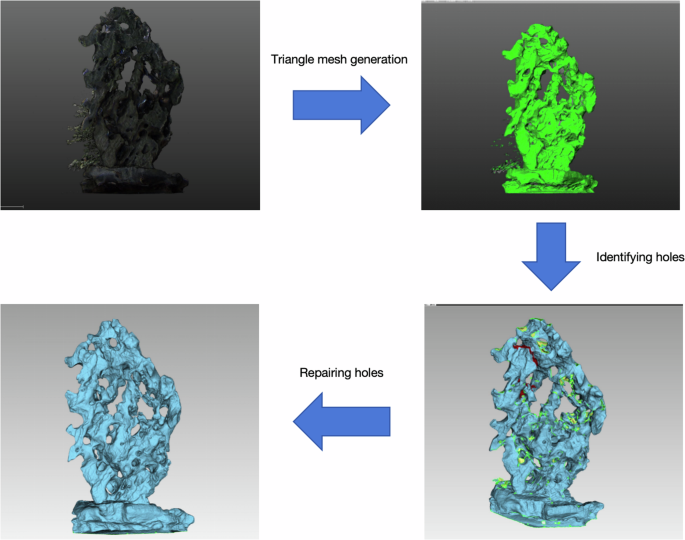
Model processing.
After the modeling was completed, a preliminary study was conducted on the texture of the main surface of Ruiyun Peak. The model accurately and meticulously reproduced the surface pores and texture features of Ruiyun Peak. The model obtained through the method discussed above was not affected by the relationship between shadow and perspective and can identify the type of texturing method with the naked eye. This study is based on the classification of textures in Zheng Ji’s “A Simple Guide to Painting from the Dream Cottage”32 during the Qing Dynasty (around the 1800s) and analyzes the texture of the surface of rockeries. Zheng Ji classified textures into 16 categories (Table 1). Therefore, based on this classification, this study compared the texture categories and conducted a comparative analysis in the point cloud model by manually identifying and marking the categories of texture and morphology. Ruiyun Peak is well known for its porous structure. By observing the main surface, the main pore parts were marked in the model, which is known as the skeleton texture (manifested as interlocking holes; this method can make the rockery look more transparent) in Chinese stone appreciation culture (Fig. 7). A large number of holes display the ethereal lightness of the stone. The undulating texture on the surface, combined with many holes, forms a flame-like dynamic, showcasing the beautiful form of the “Four Famous Stones of Jiangnan.”

Skeleton texture (blue circle).
Integrated rockeries: surface texture acquisition of Nanjing Zhanyuan’s South Rockery
The texturing method for most private rockeries in the Jiangnan Gardens has rich cave and crevice variations. For stationary 3D laser scanners, most cave areas are small and cannot be scanned; therefore, more accurate point-cloud data cannot be obtained. Due to many texturing changes that are considerably subtle at the centimeter and millimeter levels, high accuracy is required for early scanning to perform relevant research on texturing. Therefore, this study adopted a representative 3D laser scanning scheme for cracks in the Nanjing Zhanyuan South Rockery (Fig. 8) by combining a stationary 3D laser scanner with a handheld 3D laser scanner, GeoSLAM ZEB HORIZON. TRW can also process the point cloud model obtained from GeoSLAM ZEB HORIZON. Complementing the two data allows complete and accurate three-dimensional data of the rockery to be obtained, thereby documenting its texture.
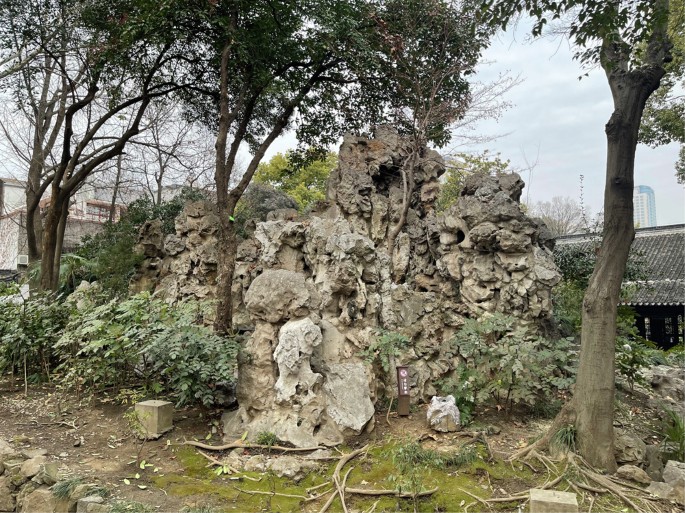
Nanjing Zhanyuan South Rockery.
After completing Zhanyuan’s South Rockery model (Fig. 9), the observation and marking of detailed mountain and stone textures were studied to mark the texturing method of the main mountain area of South Rockery. From the figure, the south rockery uses a highly rich method of mountain and stone texturing, with the most commonly used being “skeleton texture” (Fig. 10). Through stacking techniques and overlapping with holes in the rocks themselves, it retains a very transparent appearance even though the rock is large. Moreover, in addition to the skeleton texture, a large number of veins resembling the veins of a lotus leaf are still marked, which is called “lotus leaf texture (Manifested as the veins of inverted lotus leaves, spreading from top to bottom in all directions, with lotus leaf stems and stems at the top of the mountain and lotus leaf lips at the foot of the mountain, commonly used to depict mountain peaks):” (Fig. 11). The lotus-leaf texture displayed through the stacking of stones and the matching of the gaps and textures of the stones can express the artistic conception of a mountain range resembling a real mountain. Many zigzag textures were discovered through observation models at the bottom of the mountain, also known as the waterfront. These textures are mainly stacked based on the square shape of the stones themselves, resembling a folded band called the “zigzag texture (Manifested as a zigzag shape, used to represent square stones, mainly horizontal lines, usually used to refer to the texture and structure of the waterfront)” (Fig. 12). Through this texture, the feeling of the natural waterfront’s ups, downs, and folds can be restored as if entering the real waterfront.
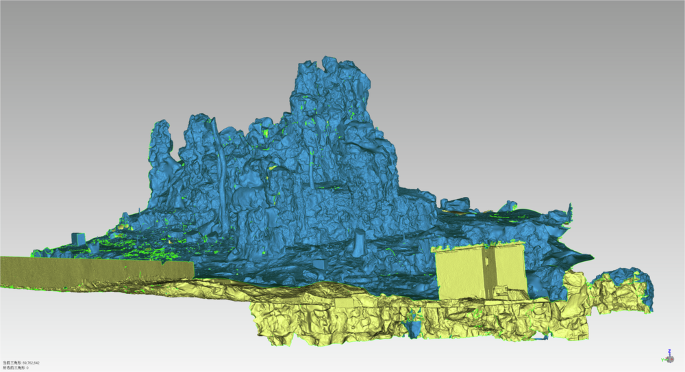
Model of Nanjing Zhanyuan South Rockery.
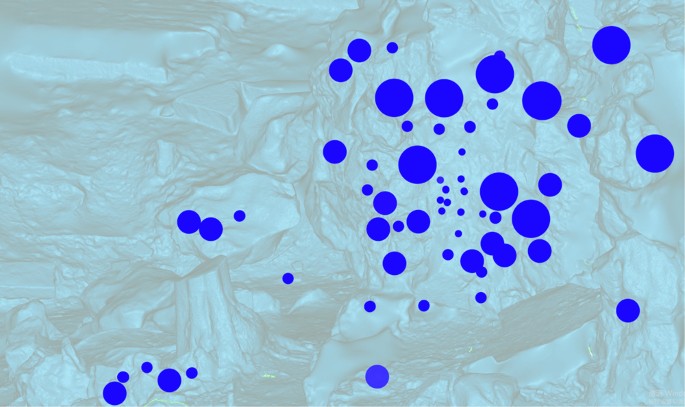
Skeleton texture (blue circle).

Lotus leaf texture (red line).
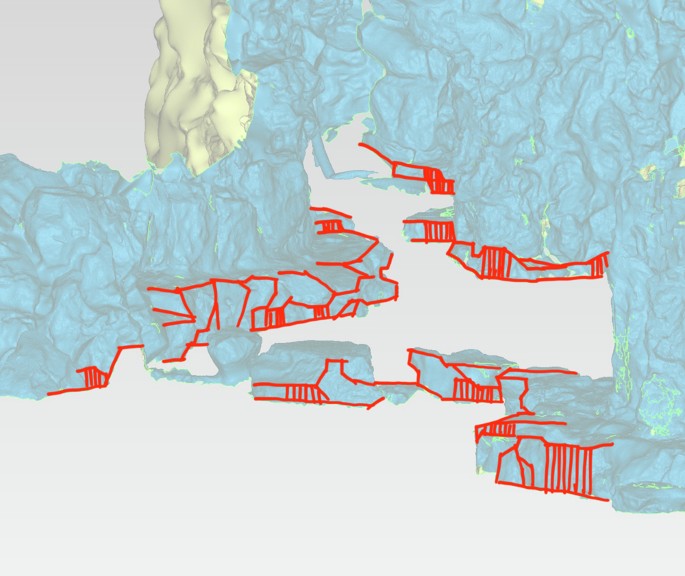
Zigzag texture (red line).
Due to the different and complex textures of rockeries, this study selected areas with more obvious texture features as examples in texture analysis and research. The main focus was on identifying and comparing the main texture features of different areas, and these textures were interwoven, ultimately forming rocks with rich forms and textures. It enriches the landscape level of the rockery texturing method by combining the skeleton texture with porous structures and different texturing methods with line and curve shapes. This approach demonstrates that the combination of stationary ground 3D laser scanning and handheld 3D laser scanning can provide complete, clear, and accurate information about the overall rockeries in Chinese gardens with complex environments and rich stone textures, and it is helpful for subsequent manual comparative analysis.
Integrated garden rockeries: surface texture acquisition of Suzhou Master-of-Nets Garden Rockery
In addition to research on the texture of the detailed surface, applying the same collection method to the texture of the overall mountain-shaped rock will take too long, and the data volume will be significantly larger. Because of the rich spatial changes in the large-scale rockeries in Suzhou Gardens, most have multiple tourist routes where tourists can shuttle back and forth. Like the Lion Forest Garden in Suzhou, many rockery stones constitute the main tourist spaces throughout the garden. The rockery is considerably large, and the route is complex. Therefore, for such a large volume of Suzhou Garden rockeries, collecting 3D scanning data using a standing ground 3D scanner as the main body is relatively complex, and many narrow and blocked areas cannot be scanned, making scanning more difficult. Handheld 3D scanners have the advantages of being lightweight and small, facilitating fast data collection, and being able to follow user movements. Its scanning distance can reach 100 m with a scanning speed of 300000 points per second, and an acquisition accuracy can be controlled within 10–30 mm. Large-scale rockery areas with complex spatial environments and tourist routes are suitable for the data collection of overall rockery morphology. This study used the Master of Nets Garden (Fig. 13) as an example to extract and analyze the overall texture of a rockery, which can be referred to as a landscape texture. The collection of rockery data is primarily based on the “Yungang” large rockery, and other lakes, rocks, and rockeries in the park were also collected. Seven scanning sites were scanned, with total scanning times of 1 h 34 min. The total number of point-cloud points was 580 million, and the processing time of the point cloud was 8 h. The resolution of the final model was 10 mm (distance between points in spatial sampling).
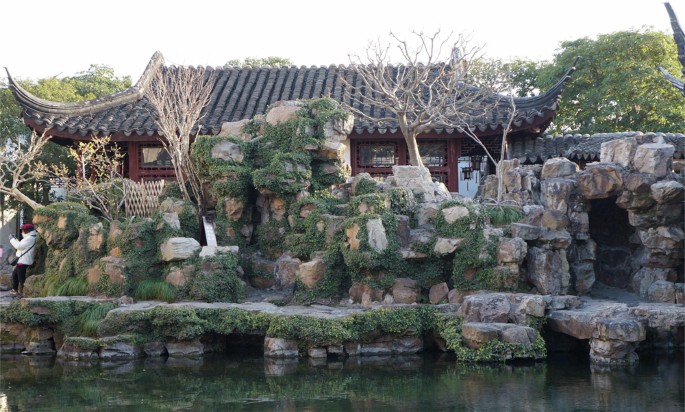
Rockeries of Master-of-Nets Garden.
After scanning the Master-of-Nets Garden, the site was spliced, a point cloud was generated (Fig. 14), and the point cloud was sliced and analyzed. By identifying the rockery texture in the Master-of-Nets Garden, it can be observed that the entire park has a rich use of rockery texture. From the front view of the main “Yungang” rockery (Fig. 15). By comparing the types of lines in the model with the classification of textures in the previous text, it can be observed that different texturing methods were used in the upper and lower parts to depict the outline of the rockery. Vertical textures were used in the upper part to highlight the height of the mountain. This texture is called “axe splitting texture” because it resembles the cracks carved by an axe. The texture is smaller and square at the bottom of the rockery, resembling horse teeth, known as “horse tooth texture.” Owing to the small space of the Master-of-Nets Garden, the process of stacking rockeries adheres to the principle of using limited rockery space to cooperate with buildings and structures. It expands the depth of the landscape, avoids blockage caused by the small garden space, and achieves the goal of changing the scenery step-by-step. Therefore, the overall texture was mostly a complex, cohesive whole formed by combining different textures. In summary, handheld 3D laser scanners can conveniently and rapidly collect information on the stacking of rockeries in Suzhou gardens. They can also collect and analyze information on the stacking method of yellow stone, which has a relatively single texture and a large volume.
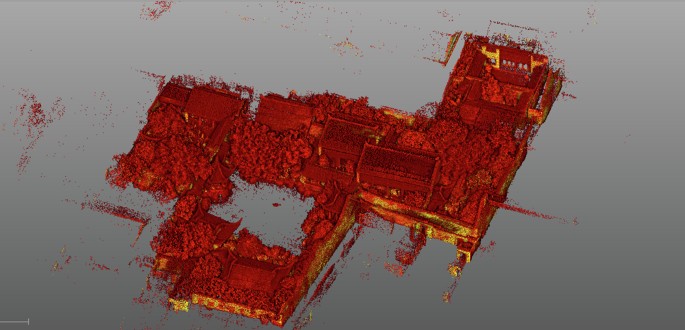
Point cloud of Master-of-Nets Garden.

Axe splitting texture (blue line) and horse tooth texture (red line).
From the above research, different scanning and point cloud acquisition methods reveal that 3D point clouds can restore the surface texture of various categories of traditional Chinese garden rockeries, which can inform texture acquisition studies. This approach provides a scientific research method for studying and documenting the texture of traditional Chinese garden rockeries, providing a scientific basis for subsequent archeological research and real-time records of rock texture research for archeologists.
3D printing
The texture obtained using this method can provide relevant data for archeological research on traditional Chinese garden rockeries. However, several archeological studies require on-site work on rockeries, such as close-range field investigations, teaching, archeological and heritage research on preserving rockery textures, and other possible heritage interaction work. Due to the rockeries’ geographical limitations, such as being located in the center of a pool, texture inspection cannot be performed in close proximity. Moreover, rockeries are immovable cultural relics that cannot be used for movable displays or archeological research. This is unfavorable for subsequent heritage and archeological research, limiting research on heritage itself. However, there have been cases of using 3D printing to replicate rock cultural heritage or archeological sites, which has many advantages. First, 3D printing allows the creation of accurate and detailed physical replicas of cultural heritage sites, cultural relics, and architectural elements, assisting with the research and preservation of cultural heritage and popular science education. These replicas can serve as teaching resources for archeology and provide interactive and immersive experiences for researchers, educators, and the public, thereby enhancing their understanding and appreciation of cultural heritage33,34,35,36. Additionally, 3D printing contributes to the dissemination of cultural heritage, enabling people to have wider exposure to and interact with historical and traditional artifacts37,38.
Furthermore, 3D printing technology contributes to the preservation and protection of cultural heritage by replicating and preserving historical and traditional artifacts, particularly those that are fragile, difficult to access, and at risk of damage or loss37. It allows replicas to be created for detailed research, analysis, and protection while preserving the original readability of historical sites or elements39. In addition, 3D printing supports the restoration of cultural heritage buildings and elements, provides innovative technologies for architecture and restoration, and addresses common anomalies in cultural heritage buildings40. However, there is limited research on 3D printing for heritage sites such as rockeries, which are large and have rich surface textures. It is necessary to restore the volume of rockeries to the maximum possible extent without losing the accuracy of their surface textures and design printing issues related to structure, materials, and other aspects. As demonstrated in previous studies, in the model processing for Ruiyun Peak and Zhanyuan, an accuracy of 1 mm is required to reflect the detailed texture of the rockery. At the same time, some 3D printing materials and methods cannot achieve printing accuracy, such as the centimeter-level printing accuracy of microcement. Due to limitations caused by the size of the printer, if the model is excessively reduced for overall printing, it can be replicated in the overall shape of the rockery. Still, the details cannot be observed because the model is too small. Therefore, this study attempted to use a 3D printing method that conforms to splicing to 3D print large rockeries, thereby providing a new type of movable heritage display by restoring the original appearance of the rockeries to the greatest extent possible.
This study selected Ruiyun Peak to implement the 3D printing method research. First, because Ruiyun Peak is located within Suzhou No.10 High School, which is not open to the public most of the year, and the rockery is located in the center of the pond, it cannot be displayed to the public, nor can it be observed for texture and archeological research. These factors have hindered archeological research on Ruiyun Peak. Therefore, this study attempts to 3D print and reproduce it to meet the external display needs of heritage and the sustainability of subsequent research. Considering the printing materials’ structural stability and practical effects, this study attempted to achieve a 1:2 3D printed replica of Ruiyun Peak. The total height of Ruiyun Peak is 6.5 meters, its width is 1.7 meters, and its thickness is 0.8 meters. SLA stereolithography was adopted to maximize the restoration of the surface texture of Ruiyun Peak. Compared with 3D printing methods such as FDM, this printing method can restore the detailed texture of the rockery surface with a processing accuracy of 0.2 mm, thus meeting the needs of archeological research. Polishing treatment was carried out on the model’s surface to make the surface texture clearer and avoid the discoloration caused by sunlight exposure. Therefore, the Union Tech Lite 800 device, which can handle a printing range of 800 mm × 800 mm × 500 mm, was used for this printing. Owing to the size limitation of the printing scale, this study adopted a segmented model approach (split the model into many smaller pieces of suitable size for printing and print these small blocks) for step-by-step printing and finally performed overall stitching to restore the current state of the rockery to the maximum extent possible without losing model accuracy (Fig. 16).
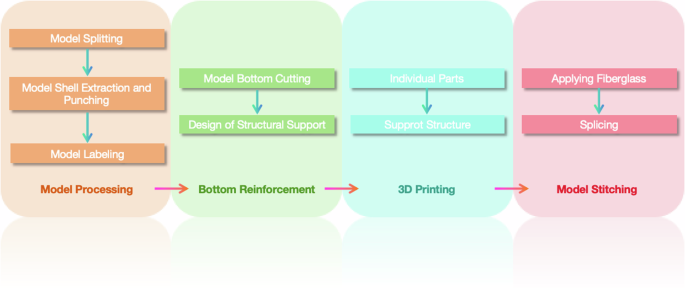
Model processing and printing flowchart.
Model splitting
The idea of splitting is to select a large, flat outer surface for easy bonding, polishing, or other treatments. Overall, layering and splitting should be performed according to the height of the printing equipment, and suitable positions should be selected within the printing range for division into large pieces. The specific cutting method uses the segmentation line function of the Magics21 software by selecting the appropriate position and size and then cutting the model with line segments. First, the Z-axis direction was cut according to the maximum printing height of the printer of 380 mm (Fig. 17a). Subsequently, in the X- and Y-axis directions, the entire structure was divided into layers, and appropriate positions within the printing range were selected according to the height of the printing equipment (Fig. 17b). Owing to bottom-up splicing, the specific cutting positions for each layer were selected from the angles and positions that were convenient to handle from above, and areas that could not be manually processed were avoided as much as possible (Fig. 17c). To avoid texture loss during the stitching process, we avoided cutting areas with complex textures during the model cutting process. We attempted to ensure the integrity of the printed complex texture areas. Owing to the large size of the model, significant splicing was required. In the subsequent stages of designing professional structures, such as insertions and tooth profiles, the splicing sequence was considered, which is not sufficiently flexible and may lead to more problems in actual splicing. Therefore, a simple flat-cut structure (Fig. 17d) was selected, and the splicing area was increased to facilitate positioning using flexible positioning pins. These flexible positioning pins were distributed on the cutting surface of the model, and their positions could be arranged accordingly (Fig. 18). Finally, the cut model was obtained (Figs. 19, 20).
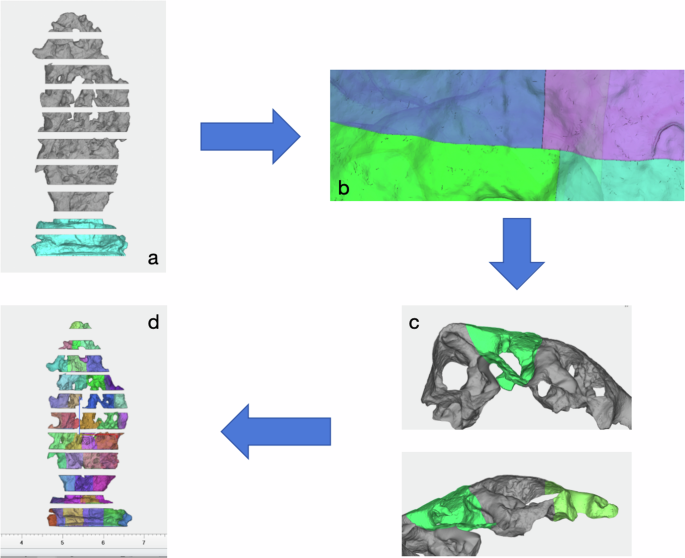
Model Splitting.
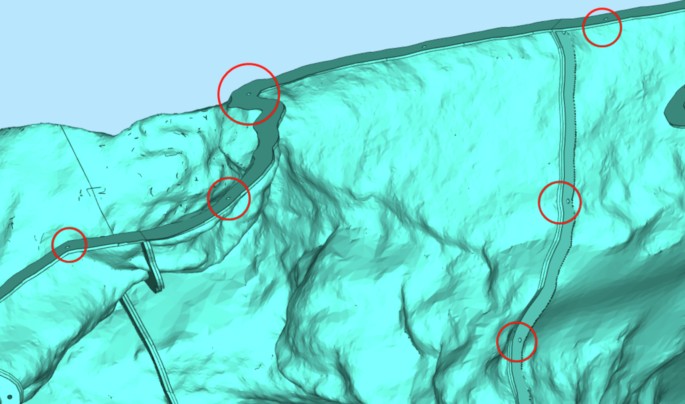
Flexible positioning pins (red circles).
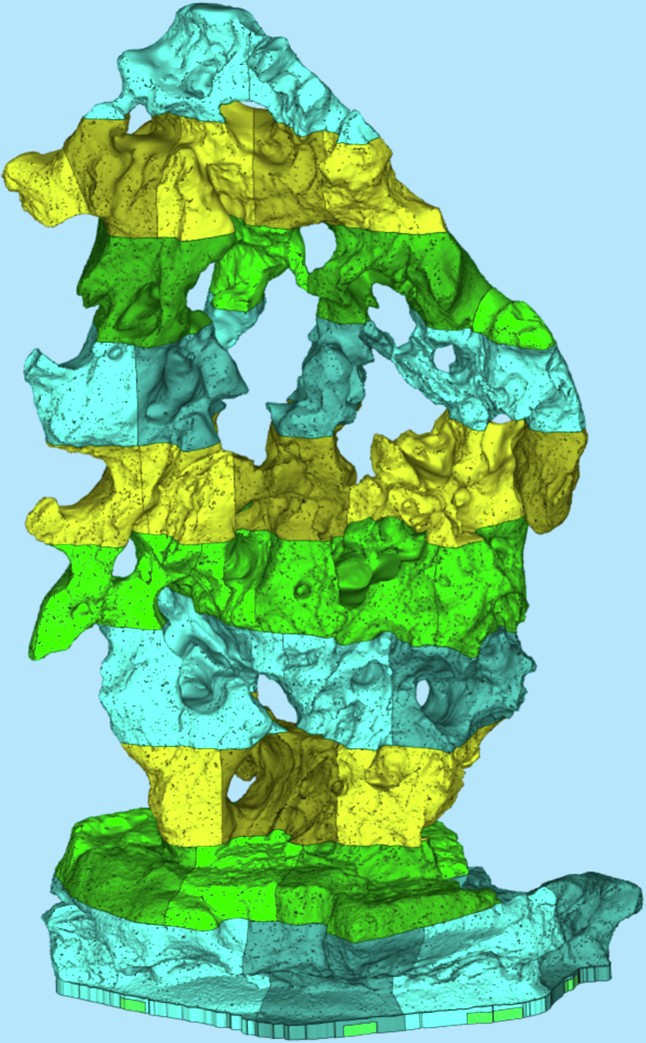
The front of the model.
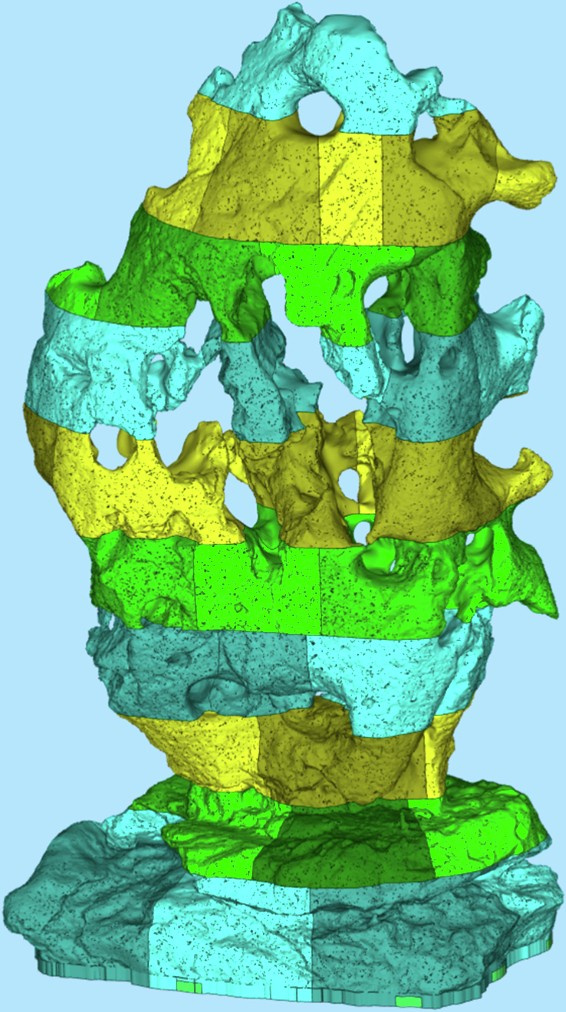
The back of the model.
Model stitching
Owing to the placement of Ruiyun Peak as an entire rock inserted into the base and considering the structural stability of the 3D printed splicing, it was necessary to perform a specialized structural reinforcement design at the bottom of the model. The base and interior required a large support space, and using wooden or mechanically processed materials was expensive. Furthermore, it was heavy and difficult to move. Due to the limited strength of the resin material used in SLA, there may be a risk of collapse after the overall assembly. Therefore, higher-strength materials must be used for structural reinforcements in the base part, where stress is concentrated. Therefore, a metal rod bracket was used for the load bearing, and a buckle was designed in an inconspicuous position at the bottom. The connecting parts were 3D printed using PLA material. First, a model with a wall thickness of 20 mm was used to facilitate the production of connecting structures (Fig. 21a). The bottom opening was then cut. Due to printer size limitations, the bottom was divided into two layers. When cutting, the small parts should not be cut separately (Fig. 21b). We chose a relatively flat position for cutting at the bottom layer while also considering the size of the printer (Fig. 21c). After cutting, each piece was individually selected with a 3 mm inner surface shell to generate edge surfaces for splicing (Fig. 22a). The buckle position was designed at the bottom (Fig. 22b), and holes were left at appropriate positions on each splicing surface (Fig. 22c). To reduce weight, a hollow stainless-steel pipe with a diameter of 15 mm was selected as the bottom support frame. The connecting piece (Fig. 23a) was printed using PLA material. When assembling the steel pipe and connecting the piece to the base (Fig. 23b), the connecting piece was designed at the buckle position to connect to the metal pipe and ensure the stability of the model during transportation (Fig. 23c). Each piece was extracted according to the bottom layer, with positioning holes designed and marked for easy splicing (Fig. 24).
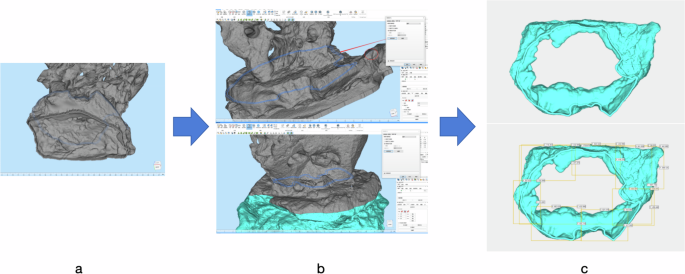
Model bottom cutting.
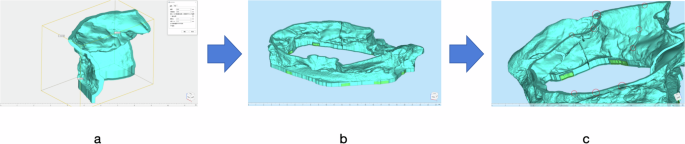
Model shell extraction and punching.
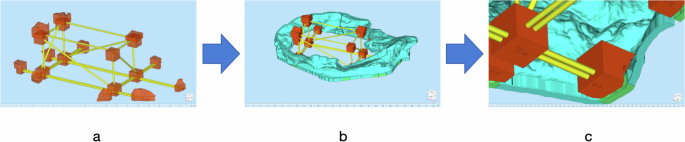
Structural support at the bottom of the model.
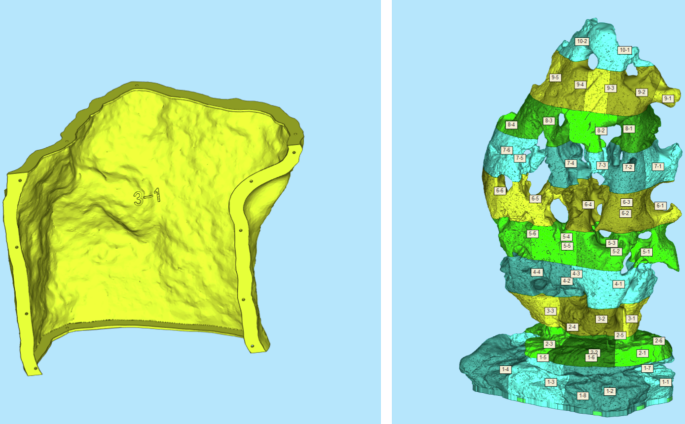
Model labeling.
Model printing
After model cutting and splitting were completed, each component was printed block-by-block and pieced together layer-by-layer from the lower layer to the top (Figs. 25, 26 and 27). Simultaneously, to ensure the structural stability of the overall model, a fiberglass material (Fig. 28) was applied inside the model to increase structural stability. The final printed and spliced Ruiyun Peak model has an overall height of 3.5 m. The printed model fully reproduced the body of Ruiyun Peak with the accuracy of texture research and could be displayed externally (Fig. 29). After the model was printed, it was placed at the China (Xuzhou) International Garden Expo as an external exhibition41. Compared to the main body of Ruiyun Peak, a 1:2 3D printing replica can achieve its public display and subsequent research by archeologists; however, its 3.5-meter model cannot be moved easily. From the perspective of heritage revitalization, it is necessary to consider how to replicate the model at different scales and achieve maximum public participation. Therefore, this study attempts to scale and print Ruiyun Peaks at 1:10 and 1:20 using an integrated whole-printing method. This method can achieve integrated whole printing, resulting in the final printing of Ruiyun Peak models with heights of 60 and 30 cm (Fig. 30), and an indoor desktop display can be achieved. It has strong mobility and can become a teaching and display mold, providing convenience to archeological learners and researchers. After the 3D printing of Ruiyun Peak models at different scales using PLA materials, this study attempted to replicate the models using metal materials. The wax loss method was used to cast Ruiyun Peak models at a height of 1:50 (Fig. 31). This replication method made the models more textured and allowed them to become cultural and creative products for the public, achieving a wider dissemination of heritage value.
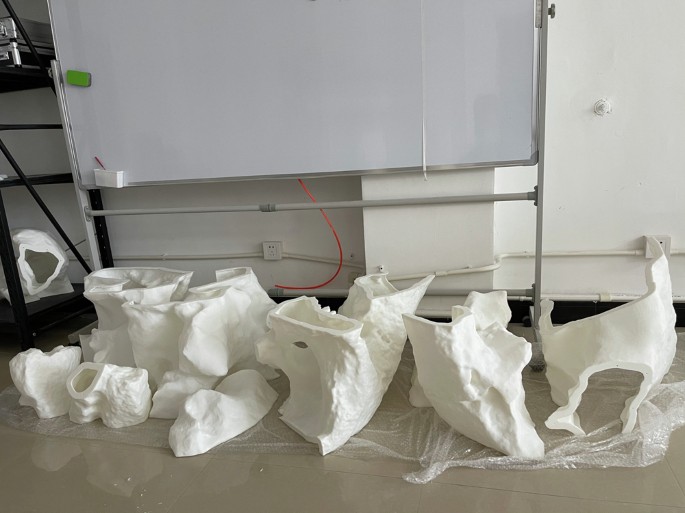
Individual parts.
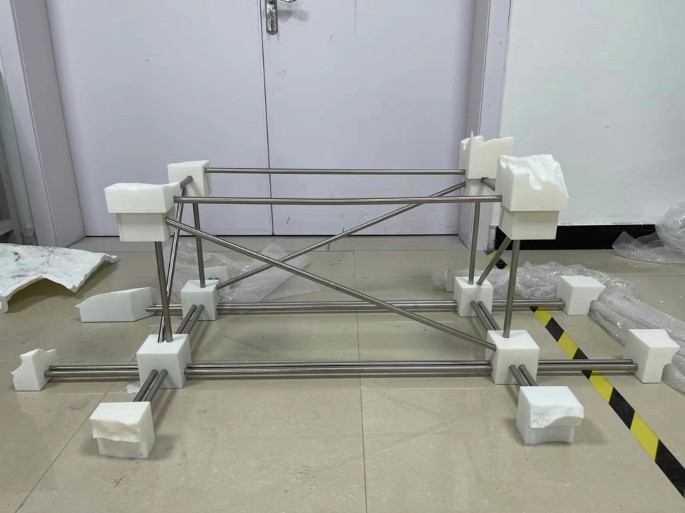
Bottom support.
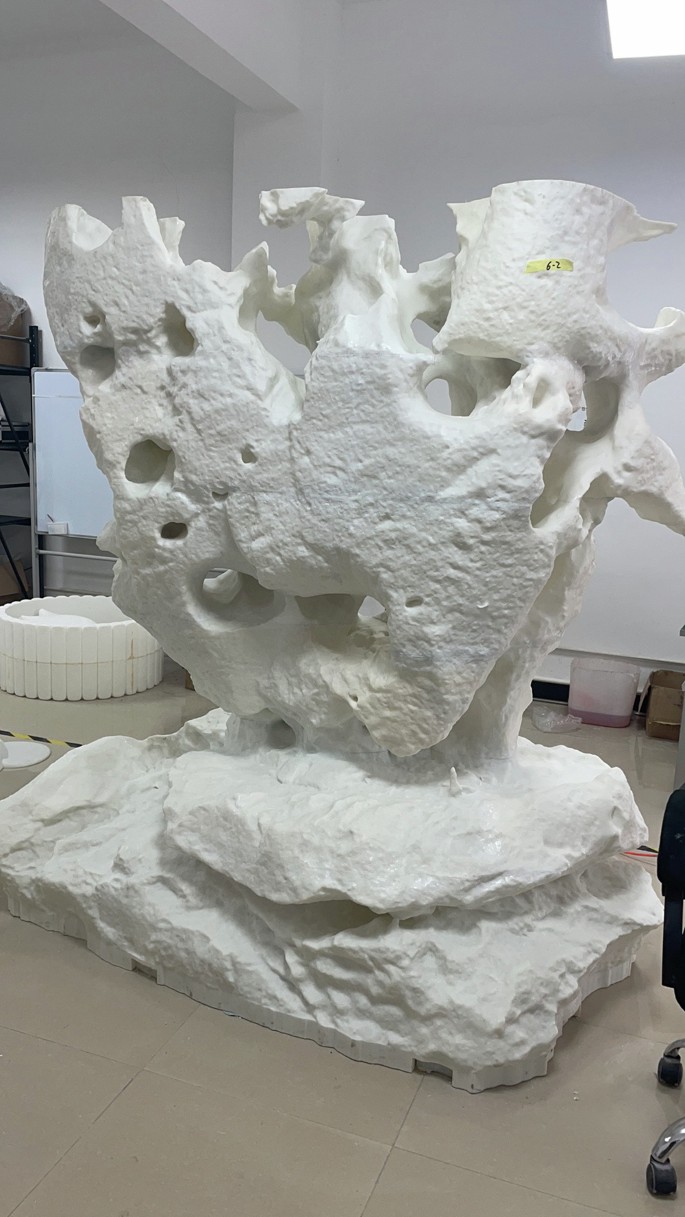
Splicing process.
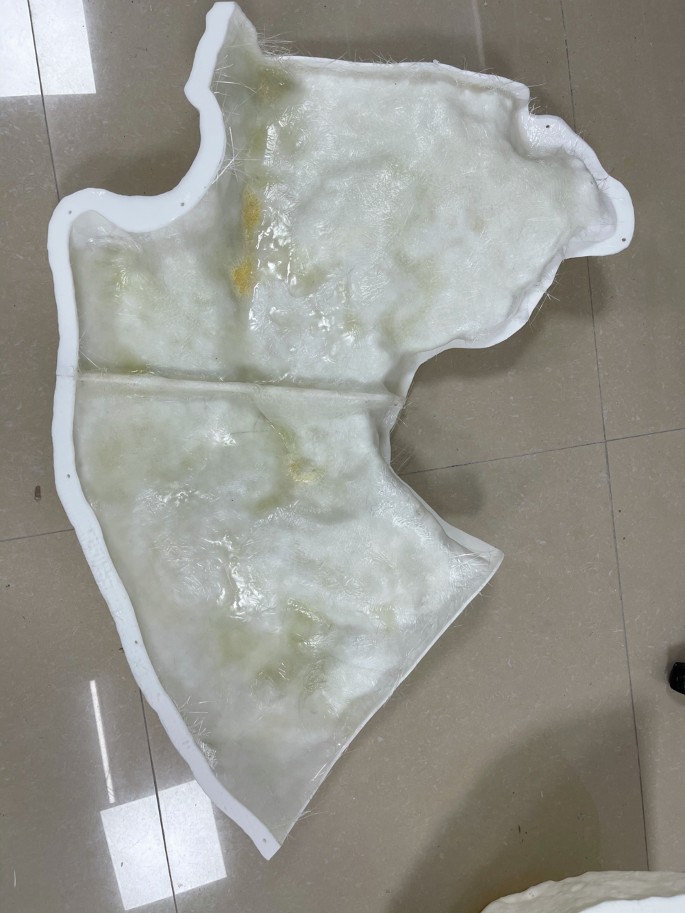
Applying fiberglass.
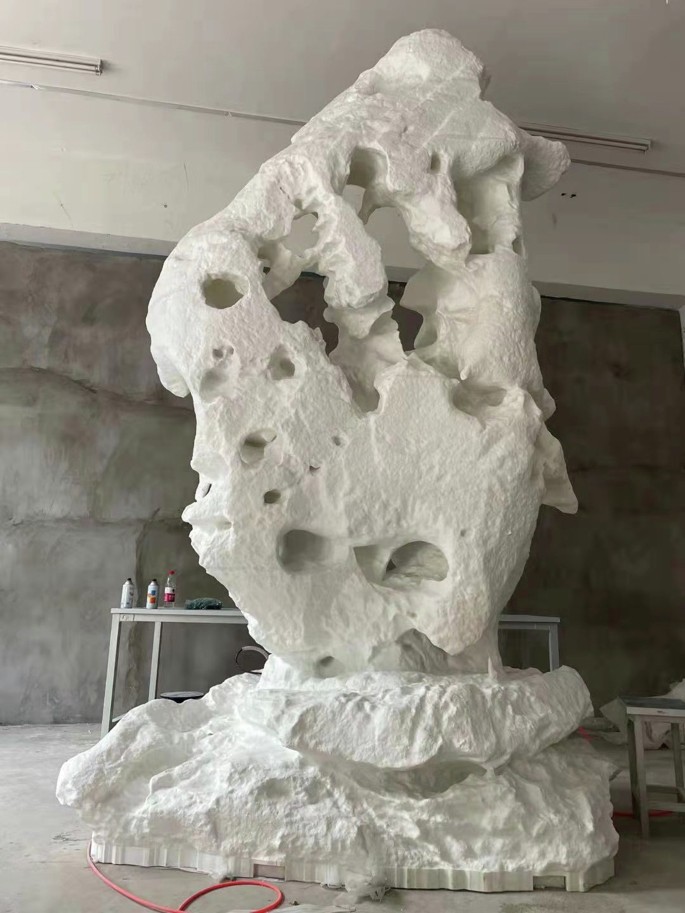
The final model.
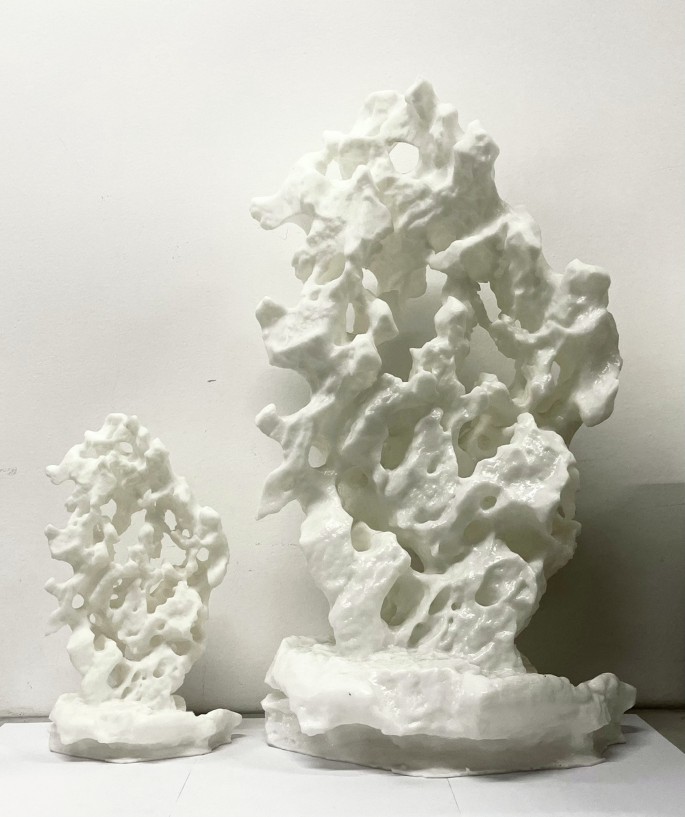
The smaller model.
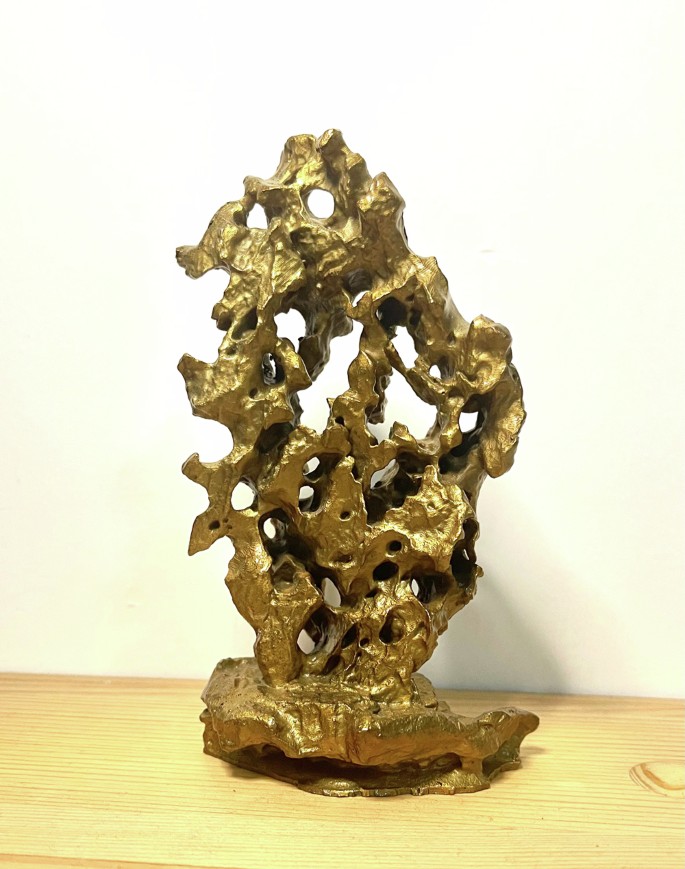
The brass model.
Results and discussion
From the three different scale research cases of texture scanning and analyses mentioned above, it can be seen that point cloud data obtained from 3D scanning with different accuracies can be specifically analyzed for different types of textures. In the research cases of Ruiyun Peak and Zhanyuan, we can see that the point cloud obtained using a stationary 3D scanner was denser. The above analysis shows that Zhanyuan’s South Rockery increases spatial richness and momentum by employing alternating changes in different texturing methods. Although it is more complex to process, it can finely identify the detailed textures on the surface of individual rocks, analyze their morphology and texture content, and produce rich textures. In the case of Master-of-Nets Garden, it can be seen that the point cloud obtained by using a handheld 3D scanner is sparser and more convenient to process than the stationary type. Compared to traditional painting and photography methods, the handheld 3D scanner is not affected by lighting and perspective relationships, and the recording speed is faster. Moreover, it is difficult to identify the overall form of large-scale rockeries through painting and photography, as the control of rockery form is easily affected by perspective relationships during the photography process, resulting in a certain degree of deviation. Additionally, too many internal elements in the garden make photography and painting susceptible to interference and obstruction from other elements. The handheld 3D scanner cannot recognize the texture of individual stone surfaces; however, it can identify the overall morphological characteristics of the rockery, thus conducting an overall modeling analysis of the rockery from a larger scale of the garden and architectural space environment. Therefore, from the perspective of studying textures of different categories, different scanning methods and point cloud processing techniques can be used in a targeted manner. When obtaining detailed textures on the surface of stones and performing morphological analysis on individual stones, a scanning method mainly based on stationary 3D laser scanning is required. After modeling the point cloud, more detailed texture data can be obtained. However, manual repair is needed in the modeling process due to the complex environment of fake rocks and the presence of many surrounding plants, which takes a long time. When it is necessary to study the overall shape of rockeries, handheld 3D laser scanners can be used for data acquisition, and there is no need to model and repair point clouds to identify more accurate rockery shapes, which can be combined with the surrounding building environment for overall analysis.
In our attempts to do a 3D printing of different materials, we found that compared to the FDM materials used in previous studies42, the SLA method has significant advantages in texture reproduction and can maximize the display of the texture on the stone surface. The brass model cast by the lost wax method also has a high degree of texture restoration, so both methods have great advantages in studying texture reproduction. However, from the strength perspective, the SLA method produces models with limited strength. It is more affected by sunlight and temperature without polishing, while brass models made by the wax loss method have better performance in strength and durability. However, from the perspective of subsequent promotion, the SLA method produces models with lower costs and more convenient mass production. From the perspective of tourism promotion, it is more suitable for secondary creation and display.
On the other hand, brass models have certain difficulties in both cost and mass production and are suitable for heritage display requirements with high demand. Regarding printing accuracy, the Union Tech Lite 800 equipment used in the SLA method can control the printing accuracy within 0.2 mm29. However, during the model-making process, the model’s accuracy may be compromised to some extent due to the need to split the print, reassemble it, and polish the surface. Therefore, this model is more suitable for use in exhibitions. There may be a certain degree of accuracy deviation in the study of millimeter-level textures. In future research, different model processing methods will continue to be considered to reduce the accuracy loss caused by printing and subsequent model processing.
Conclusion
This study systematically recorded and recognized the surface texture of digital point clouds for different types of traditional Chinese garden rockeries. It formed a systematic surface texture recording scheme, making it possible to identify the type of artificial rockery texture, which helps understand rockeries. Through this research approach, the current record of the surface texture of rockery cultural heritage sites is not limited to photographs and paintings, which provides the possibility for sustained texture research in the future. This approach provides a digital foundation for subsequent archeological and value research and archival information for heritage protection. Simultaneously, owing to the limitations of archeological and heritage research caused by the large size and complex environment of rockeries, this study proposes and uses 3D printing to achieve the replication of large rockeries, solving the problems of heritage replication regarding structure and accuracy. It achieved the first large-scale rockery model with a 1:2 replication and allowed multiscale and multimaterial printing. Due to the lack of a comprehensive protection system for Chinese Classical Garden and rockeries in China and the fact that rockeries are exposed to outdoor environments year-round, their surface textures are severely damaged43. This study provides a relatively complete method for digital replication and analysis of traditional garden rockery textures. On the one hand, it solves the digital recording problem and protecting rockery textures. It provides a modern solution for disseminating and inheriting heritage.
Furthermore, this method applies to other types of stone cultural heritage with complex surface textures, such as grotto temples, stone tablets, and large stone statues. This type of stone cultural heritage is similar to rockeries, with large volume, immobility, complex surface texture, complex environment, and long-term outdoor exposure. This study also provides a reference and inspiration for protecting and inheriting this type of stone cultural heritage.
The model of the rockery was replicated through 3D printing, which maximized the restoration of texture on the surface of the rockery and had the following advantages at different levels:
-
(i)
In the current situation, where the impact of climate change on cultural heritage is becoming increasingly severe, climate disasters, such as acid rain and weathering, have gradually caused irreversible effects on the texture of the surface of rockeries. However, rockeries are always outdoors, and the surface degradation caused by this environment is inevitable and continuous. 3D printing provides a way to preserve the surface texture of artificial mountain stones in their original state, thus enabling the physical protection of heritage sites. This study provides a reference for the subsequent repair of rockeries or their reconstruction after damage.
-
(ii)
Due to the use of natural irregular rocks in the construction of rockery heritage, it is very difficult to replicate the heritage restoration process using rock materials. If there is damage, it is difficult to repair and replace it with rocks of the same shape. 3D printing technology provides a possibility for restoration, which can reduce the duration of manual repair and restore the original appearance of the heritage to the greatest extent possible. This study provides a way to produce support materials through 3D printing, which can provide more accurate support structures. Compared to the original method of using small broken stones for structural reinforcement44, 3D printing can produce components that better fit the rockery body.
-
(iii)
With the research on preventive protection, numerous rockery heritage sites have begun to undergo heritage monitoring and protection work, which requires rockeries’ closure. Tourists’ behavior has an impact on heritage safety to a certain extent. Therefore, there is a certain degree of contradiction between protecting heritage sites and revitalizing heritage tourism. By displaying 3D models, it is possible to reduce the interaction between the audience and the rockery to a certain extent. This reduces direct contact between tourists, the original heritage site, and the model without affecting the exhibition. Simultaneously, this approach can provide convenience for more researchers who may not be able to conduct on-site inspections while also preventing damage to the heritage site due to archeological and heritage research.
-
(iv)
Archeological research on textures has always been conducted on the same scale. Different printing scales achieved through 3D printing can provide different research scales for subsequent research, allowing researchers to observe and analyze the texture of rockery surfaces from different perspectives and scales and reveal more macro-level artistic styles and structural characteristics.
-
(v)
In recent years, many rockery heritage sites have had to be closed due to safety concerns, making education and learning about rockery heritage very difficult. 3D printed rockeries can, to some extent, replace the original rockeries to provide online and offline resources for learning and education by assisting with the education and inheritance of heritage so that more people can understand and learn about rockery heritage. Small models can be conveniently displayed in museums with limited space, thus enhancing heritage sites’ educational value and interactive experience.
-
(vi)
Through 3D printing, different materials can be used for the secondary creation of rockery heritage, providing more creative space for heritage tourism. Heritage managers can rapidly mass produce cultural and creative products through 3D printing and create tourism IPs through the secondary creation of models, thereby generating more income and providing more assistance for the sustainable development of heritage.
In summary, integrating 3D point-cloud technology and 3D printing has significantly promoted the recording, identification, and replication of large-scale rock cultural heritage and archeological sites, particularly the cultural heritage represented by surface textures. This digital recording method overcame the research dilemma of traditional Chinese garden rockeries. The use of 3D point clouds enables the accurate and detailed recording of surface textures, which helps to protect and understand the cultural heritage of garden rockeries. The application of 3D printing technology has promoted the replication of these rock sites, allowing for the creation of tangible and immersive replicas, which can be used as valuable teaching resources that enhance public participation in archeology. The combination of these technologies supports the preservation and protection of cultural heritage and extends to educational and research applications. This provides innovative solutions for maintaining and disseminating historical and traditional cultural relics.
From the perspective of heritage revitalization, in future research and applications, the combination of 3D scanning and 3D printing can be used to attempt the secondary creation of rock heritage, allowing these immovable cultural relics to be understood by more people in a more modern and artistic way. Large-scale 3D-printed replicas can be combined with lighting and other methods for tourism exhibitions, thereby achieving the purpose of cultural promotion and inheritance. At the same time, 3D printing enables high-precision mass production of rock heritage sites with fine textures, enabling cultural and creative design and sales, bringing income and creativity to the heritage site itself. From the perspective of heritage conservation, 3D scanning records and analyzes the texture of rock surfaces to the greatest extent possible and can be disseminated worldwide, which is of great significance for the protection and inheritance of such cultural heritage. The fine replication of 3D printing also has a certain possibility in restoring rock cultural heritage in the future. In this study, the main research object is the texture and morphology of rockeries; therefore, this research chose to omit information on the color of the rockeries.
Regarding material selection for 3D printing, the study attempted to select materials with colors for printing, such as brass models, which still have a single-color effect and cannot restore the natural color of rockeries. In terms of the color reproduction effect, manual coloring in the later stages can be better at restoring the stone’s original color than monochrome models. However, this manual coloring method still has subjective processing factors. Therefore, this study retained the original color information of the rockery in the point cloud model. In future research, we will continue to explore how to directly assign color information to the model during 3D printing, thereby forming an integrated high-precision 3D model with the original color of the rockery. Research on achieving greater interaction between people and cultural heritage through virtual reality may also be a major research direction in the future.
Responses